Things you should know about Galley Maintenance Plans
The importance of having a comprehensive maintenance plan in place has become commonly recognized in the marine industry. On this, we all agree. The confusion starts when we sit down to pin out what maintenance plan to choose and what the right reasons are for choosing a certain plan.
Blog post by Nicolas Lesbats, VP of Maintenance Service Division at ALMACO
Maintenance comes in many forms: corrective, preventative, planned, automatic, predictive, condition-based, risk-based, and so on and on. And to make it even more complicated to get an overview, many of these maintenance types overlap each other! But no worries, they can be roughly divided into two groups, corrective and preventative maintenance. Corrective maintenance is fairly simple, “run-to-failure”, and there are not many variations on how the set up a corrective plan. Preventative maintenance, on the other hand, is about anticipation, and this model can be laid out in numerous different ways. Let us dive in for a closer look at the alternatives.
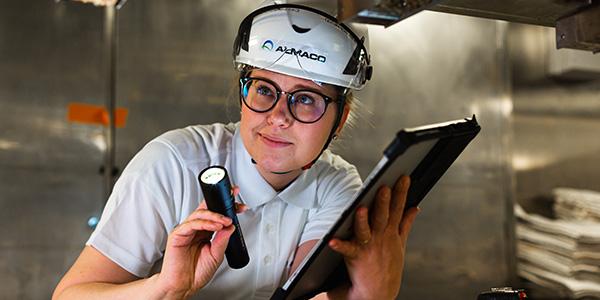
CORRECTIVE MAINTENANCE
With the corrective maintenance or “run-to-failure”, the strategy is to wait until a failure occurs before reacting. No anticipation. This method is the most commonly used, in our and many other industries, for the simple reason that it does not require an organization, processes, management tools… etc. Corrective maintenance is widely accepted as the best option to minimize short-term maintenance costs. And yes, this method does minimize direct costs, but it also has some disadvantages and indirect costs. For instance, a sudden catering equipment failure can force a restaurant onboard to adapt and reorganize the workflow in the galley to work around the failure. This can cause stress and loss of time and efficiency, and it might even force the galley crew to take some dishes off the menu . Ordering new equipment, service or spare parts in a rush is seldom the most economical way to fix a problem in the long run.
PREVENTATIVE MAINTENANCE
Instead of waiting for a failure to happen, a preventative maintenance plan is designed to anticipate and avoid failure before it happens. There are many ways to do this and the biggest difference lies within deciding when and how to intervene before the failure.
PLANNED CONDITION-BASED MAINTENANCE
Based on typical running hours, intervention is planned every X period of time. This type of maintenance does not use any digital monitoring systems such as data collection of actual run hours, rotation, etc. It follows a calendar and most likely, intervention happens before the equipment fails.
TIME-BASED MAINTENANCE
With time-based maintenance, some equipment data is monitored. The most common data to collect in galleys are running hours. Like with a car, we can plan to intervene e.g. every 6 months or 1000 hours, whichever comes first. The intervals are irregular, but this method allows higher performance and lower downtime and thereby decreases the risk of equipment failure even further.
PREDICTIVE MAINTENANCE
The galley equipment has sensors that collect physical data, for instance a vibration sensor on an electrical motor. When a certain vibration level is reached, a warning notification pops up that a failure is about to occur.
Many feel hesitance about implementing a predictive maintenance plan. Why? The main inconvenience comes right in the beginning. A predictive maintenance plan requires an initial implementation investment. The numerous benefits of predictive maintenance come later, with operation time.
Implementing a predictive maintenance plan drastically extends the lifetime of the equipment, while reducing the consumption of spare parts. The total cost of ownership, including the purchasing price, spare parts, and service, is significantly lower.
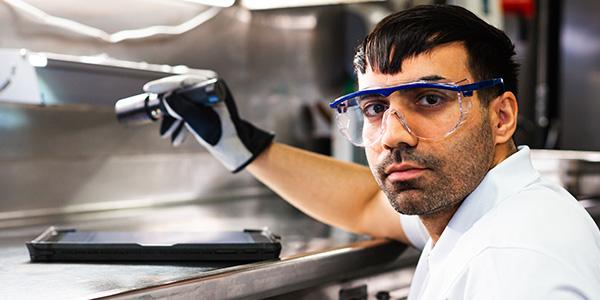
CONCLUSION
Many owners choose a maintenance plan consisting of different maintenance types for different equipment. As a thumb of rule, one could say that the more expensive, hard to get and crucial for operation a piece of equipment is, the more important it is to have a predictive maintenance plan in place for that piece of equipment.