LIFECYCLE CONCEPTS THAT EASE OPERATIONS AND REDUCE CARBON FOOTPRINT
The maintenance turnkey business model is increasingly adopted in the marine industry to consolidate multiple brands and improve efficiency while reducing costs and carbon footprint. ALMACO has a proven track-record of successfully applying turnkey lifecycle concepts in galleys and other hotel technical areas with excellent results.
OUTSOURCING AND CONSOLIDATION
As a project turnkey provider in Catering, Laundry and Accommodation, along with being a specialized Marine distributor, ALMACO has proven its value to the industry. More and more cruise, expedition, and ferry owners are now also relying on ALMACO to carry out some level of maintenance turnkey services in their galleys.
6 YEARS OF TURNKEY LIFECYCLE CONTRACTS
The journey started in 2018, when ALMACO decided to enter the maintenance field. Back then, the industry was still relying almost exclusively on reactive and corrective maintenance in galley areas, similar to other below-decks systems some 10-15 years ago.
Our cruise line customers have repeatedly told us that maintaining galleys and other hotel technical areas is a must to ensure superior passenger service. However, this task often falls outside their core expertise, and managing fragmented assets adds to the challenge.
ALMACO makes this complexity look easy
Post-COVID, ALMACO’s turnkey maintenance offering has gained traction among the ship owners facing fleet restart challenges. Why is this? Because there are just too many brands, too much equipment and too much associated data to be efficient if you are not an independent expert with the proper tools. This is where ALMACO enters the scene. We have the tools and expertise to take on turnkey lifecycle contracts while making it look easy.
Want to learn more?
Contact us for more information about our Lifecycle Service Concepts.
The recipe for a SEAMLESS maintenance
Though intuitively appealing to owners, outsourcing some of their galley maintenance seemed like a leap of faith in the beginning. However, after the first year of outsourcing maintenance, the experience has been overwhelmingly positive for several owners within the cruise, ferry, and expedition sectors. With a track record of several years providing and renewing this service, we can proudly say that no customer that has started this journey with us has later decided to discontinue it.
So, what’s the secret? The core of the solution lies in planning and consolidating the yearly maintenance cycle of multiple brands and equipment types.
With our solid reputation, ALMACO has a unique position. As an independent contractor with a wide expertise, we can service any galley brand. ALMACO has strong partnerships with Original Equipment Manufacturers, who encourage us to give the best support to our mutual customers.
The secret lies in multi-brand planning and consolidation.
Hervé Touzard
VP Lifecycle Services
How we reduce carbon footprint
The carbon footprint reduction stems from consolidation and extended equipment lifespan.
When ALMACO technicians service several brands at once, it dramatically reduces the number of OEMs that need to come onboard, resulting in significant savings on flights and fewer travel days. Additionally, like with any other technical systems, yearly maintenance extends the lifetime of the equipment. An additional year of use can mean a lifespan extension by 10 to 15% for galley equipment.
For galleys, which are multi-million-euro assets, this represents significant financial savings and postpones many replacements. From a sustainability perspective, the best equipment is the one that was never produced.
Note that new vessels and older ones are treated differently. On new vessels, preventative maintenance allows to maintain the equipment’s condition longer, while on older vessels, the goal is more pragmatic: a combination of corrective and preventative maintenance to improve equipment condition.
However, the turnkey maintenance delivery does not stop there. In most cases, these planned interventions are complemented with crew training and condition-based inspection or maintenance, along with whatever services our customers see fit.
In general, owners receive ALMACO lifecycle support ranging from spare parts and equipment supply to maintenance and replacement. And ALMACO is well-known for providing extensive support as well as delivering large and complex modernizations when required.
Well-planned maintenance means less traveling and prolonged equipment lifespan by 10-15 %!
Hervé Touzard
VP Lifecycle Services
THE NEW WAY TO DO LIFECYCLE
As the cherry on the cake, ALMACO has introduced specially developed digital tools that enable scalability and efficiency. Here is how they work:
- Firstly, we systematically establish a Digital Inventory to map the equipment onboard and more importantly, ensure that this data remains up to date.
- Secondly, we make all equipment documentation accessible through a customer portal.
- Thirdly, we utilize and share a common maintenance tool with our customers, ensuring everybody has access to the latest equipment-specific information, including condition, maintenance logs, and maintenance tasks.
And this isn’t just another tool, it’s an App that is integrated with our customers’ existing systems. These collaborative digital tools facilitate information sharing between the crew and shore team, eliminating the need for outdated spreadsheets and reports flying around in emails. In a nutshell, ALMACO helps maintaining a more reliable and efficient galley onboard our customers vessels. This and so much more!
collaboration process
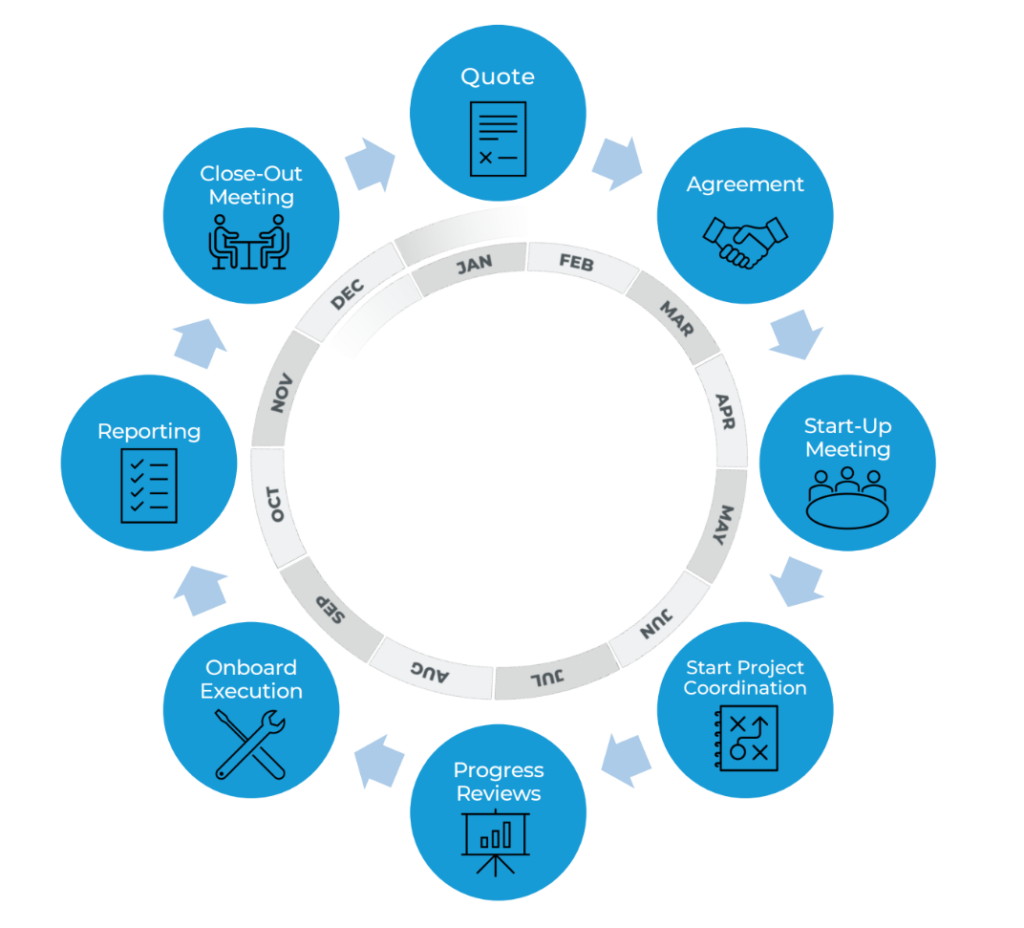
The lifecycle agreements that ALMACO signs with our customers follow a clear and simple cycle, usually initialized by a first quote to the customer.
Project coordination starts before the contract is awarded and lasts until project close-out. ALMACO maintains progress reviews throughout the whole project timeline.
During the onboard execution, our service engineers, not only replace components and diagnose issues, but also work with the crew onboard to understand equipment usage and train for routine maintenance and cleaning.
Once the maintenance is completed, ALMACO provides our customer with the agreed reports which are followed by a close-out meeting. Here, we discuss the project, reports and lessons learned to prepare for the following onboard intervention.
Let’s get started with your lifecycle plan!
FIND OUT more
For more information, contact

Contact Us
LIFECYCLE PUBLICATIONS »
ALMACO Group Rewarded With Continued Maintenance Contract For Marella Cruises
ALMACO Group is proud to announce the successful continuation of its fleet maintenance services for Marella Cruises. Marella Cruises is reconducting its maintenance contract with ALMACO for 2025, ref…
ALMACO DEPLOYS OIL CHEF’S INNOVATIVE SUSTAINABILITY SOLUTION ON FRED OLSEN FLEET
ALMACO Group and OiL Chef are thrilled to announce the successful deployment of OiL Chef’s advanced deep fryer device on Fred Olsen’s fleet of vessels. Energy savings translate to cost savings �…
ALMACO and OiL Chef announce exclusive distribution agreement for deep fryer solution
OiL Chef, the innovation award winning supplier of premium culinary eco-friendly deep frying technology, and ALMACO have signed an exclusive distribution agreement for the marine and offshore sectors…